Gary Wood from I-CAR talks about the challenged posed by mult-material body structures.
Our industry is in a state of continual change, and for many, those changes can be difficult to work with and accept. When successful businesses and reputations have been built upon existing skills and knowledge, it is understandable that there is a reluctance to accept that carrying out vehicle repairs now has to be approached with a new way of thinking and an alternative skillset, after all, it’s just another car isn’t it?
Traditional knowledge and methods to repair vehicles have been ingrained into those of us who have been involved in vehicle repair for numerous years. Repairing a component rather than replacing it simply because it has a small amount of damage has always been the accepted solution.
However, using those traditional methods to carry out repairs on a modern vehicle can be an extremely risky decision. Realigning and repairing the component can produce a visually acceptable repair. Visually is the key word in that sentence.
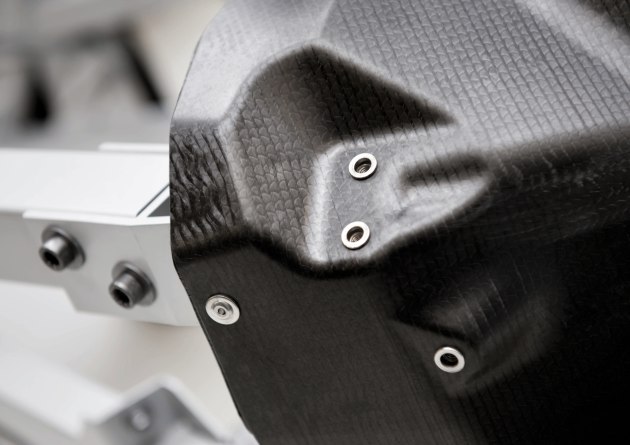
As vehicle structures become ever more complex, even minor damage to a load bearing component could potentially lead to a major failure in the vehicle structure. Any type of failure has the potential to cause significant injury or worse. A visually acceptable repair may have seriously weakened or even destroyed the structural integrity of the component, yes, it may look okay but what will happen when it is subjected to the forces from a heavy impact? That is how we must now consider every repair decision we make.
Using our traditional repair attitudes and ideas is no longer the acceptable way to carry out repairs. OEMs are providing us with more information than ever before to carry out repairs to their highly engineered vehicles.
Those vehicle structures are becoming ever more complex. With the drive towards light weighting of vehicle bodies continuing, we are seeing more and more OEMs move towards multi-material construction. Aluminium has been seen as a key material regarding this in recent years and businesses who invested in aluminium repair areas were attempting to be one step ahead of the game before full aluminium vehicle bodies became the norm.
That hasn’t panned out as expected, OEMs are now moving away from full aluminium bodies to bodies constructed from a mixture of different materials, most notably, High Strength and Ultra High Strength Steels, aluminium in various forms such as castings and extrusions, magnesium and carbon fibre are also being used more widely than we have ever seen before. This gives the manufacturer the reduction in weight but maintains the incredibly strong structure required to achieve maximum safety ratings.
These vehicle bodies have very specific repair instructions and MUST be followed accurately to ensure the vehicle is repaired safely and correctly. Structural straightening is generally not an option on multi material bodies, using a straightening system to realign a multi material body can cause catastrophic damage to the structure. This has seen OEMs who have recommended bracket type benches for years, now move to highly accurate 3D measuring systems instead.
Multi material work bays
Multi material work bays are becoming part of many OEMs approved tooling requirements. Having a designated area that will allow repairers to work safely with the various materials on modern vehicles is something that should be a vitally important consideration for any business. There are significant safety issues that have to be taken into account when working with multi material vehicles. Having the correct dust extraction system is key to a safe multi material work bay.
Using a standard vacuum type dust extraction system could potentially create an explosion due to the different materials combining under the right conditions. Aluminium particulate matter and iron oxide (rust) plus a strong ignition source can trigger a thermite reaction. The ignition source required to ignite this volatile mixture is 450°C, grinding sparks are around 980°C. Using a standard vacuum type dust extraction system without a spark arrester could easily create that ignition point. This metal fire burns at temperatures of up to 2,400°C and cannot be extinguished with water, it creates an incredibly dangerous situation.
Keeping the work area dry and using an approved sparkless dust extraction system will prevent this from happening, but the hazards are very real.
Attachment methods on these type of vehicle bodies have also got to be considered. We are now seeing different types of fasteners used by OEMs to attach the various materials. The use of adhesive is widespread in multi material vehicle bodies, this not only provides an incredibly strong bond when applied correctly but can also prevent any type of cross contamination between the components.
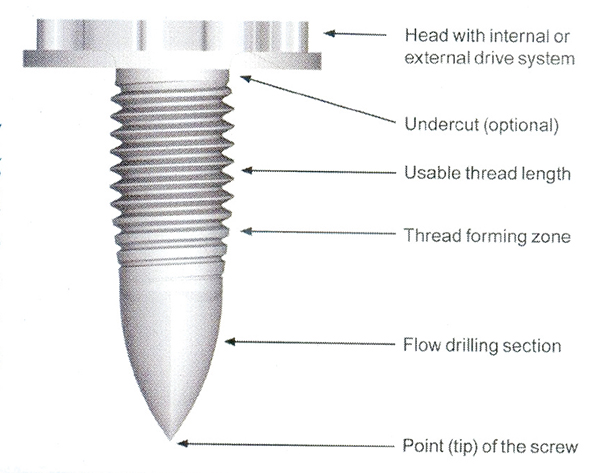
Flow drill screws (pictured), friction element welding, clinching and various types of rivets can be found across the vehicle structure. Understanding how they are applied and, more importantly from a repairer point of view, how they are replaced during the repair process are vitally important to carry out a safe and proper repair.
From repairability of the various components to safety concerns when working with multi material bodies, knowledge and understanding of the processes are becoming ever more crucial. The importance of training becomes key to understanding what is involved in any potential repair but, just as importantly, key to carrying out those repairs in a safe, controlled environment where repairers, insurers and the vehicle owners can all be confident that the vehicle will be repaired to manufacturer standards, and that it will react as expected in any subsequent accident.
No longer can we fully rely on our existing knowledge and skills to carry out accurate damage assessments or repairs to modern vehicles, after all, it’s NOT just another car.